Трубопроводы, как и любые другие промышленные объекты, при эксплуатации попадают под негативное воздействие окружающей среды. В результате, на поверхности и в полости изделия могут образоваться коррозии, трещины, сколы, неоднородные среды и другие виды дефектов. Кроме того, даже новые трубопроводы и трубы могут иметь изъяны, несмотря на применение современных технологий в производстве. Для выявления дефектов и предотвращения серьезных последствий используют ультразвуковые методики контроля. Самым эффективным для контроля и выявления дефектов в элементах трубопроводов считается ультразвуковая дефектоскопия, или УЗК.
Ультразвуковой контроль применяют на теплосетях, газоподающих сетях, нефтепроводах, водоподающих трубопроводах. При помощи этого метода можно обнаружить:
— потерю уровня герметичности;
— потерю контроля состояния напряженности;
— нарушение сварных стыков;
— разгерметизацию сварных швов.
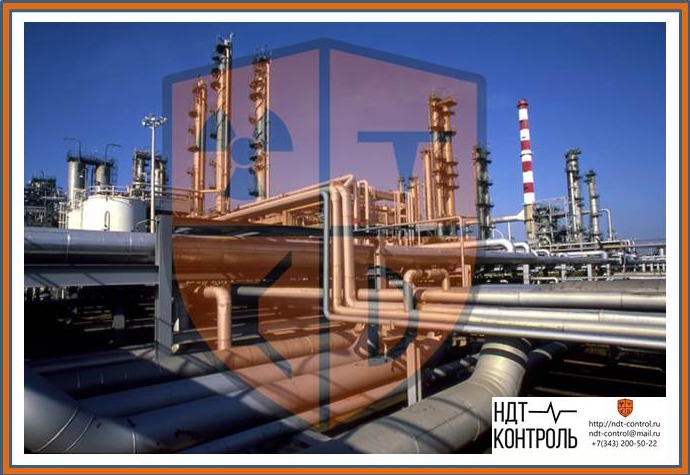
С помощью УЗК трубопроводов можно определить размер дефекта, расположение, а также качественное состояние швов и сварных элементов. УЗК выявляет следующие показатели:
— уровень прочности элемента;
— степень антикоррозийной устойчивости;
— пластичность объекта;
— структуру металла шва и области возле него;
— количество и габариты дефектов.
Следует отметить преимущества дефектоскопии трубопроводов:
- минимальные временные затраты на процедуру контроля;
- высокая точность полученных данных;
- приемлемая стоимость;
- отсутствие рисков для жизни и здоровья человека;
- мобильность и компактность оборудования для УЗК;
- проведение контроля качества без остановки производственных процессов, отключения исследуемых и сообщающихся объектов (то есть, нет необходимости останавливать или изменять работу оборудования на предприятии).
Способы обнаружения дефектов и неисправностей в трубопроводах все время совершенствуются, создается более эффективное оборудование, в том числе, новые модели дефектоскопов. Постоянно проводятся различные исследования в данной области, направленные на улучшение работы средств контроля.
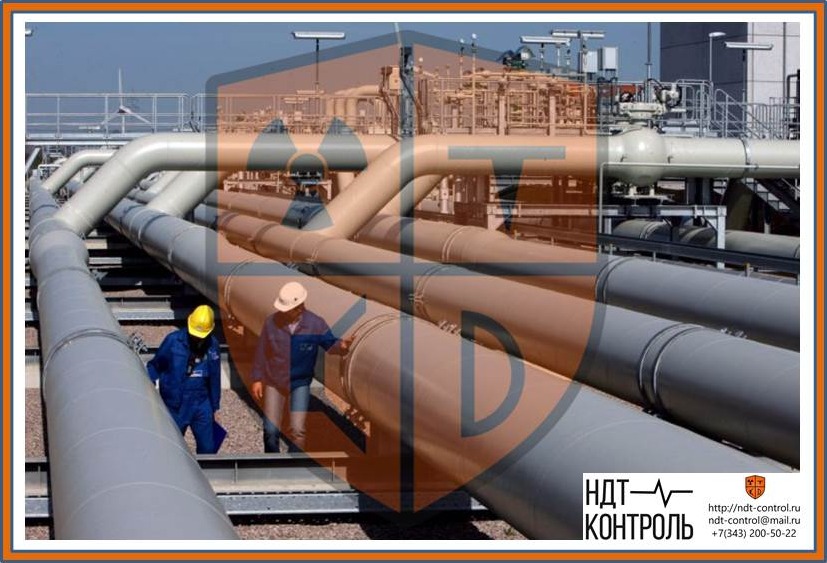